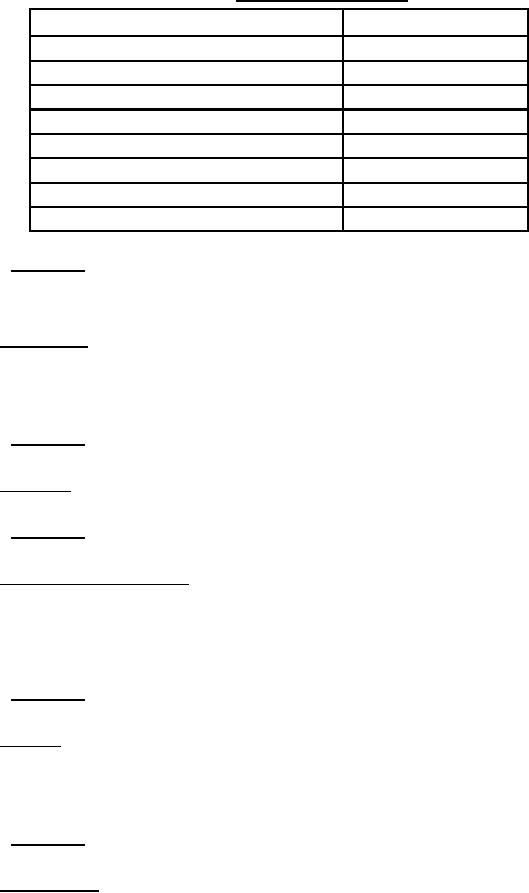
MIL-DTL-24643C
TABLE XIV. Immersion test temperatures.
Fluid
Test temperature
Fuel oil, MIL-DTL-16884
98 to 100 °C
Turbine fuel, JP-5, MIL-DTL-5624
48 to 50 °C
Cleaner, isopropyl alcohol, ASTM D770
20 to 25 °C
Hydraulic fluid, ADS-69-PRF
48 to 50 °C
Hydraulic fluid, MIL-PRF-17672
48 to 50 °C
Lubricating oil, MIL-PRF-23699
98 to 100 °C
Coolant, Monsanto Coolanol 25 or equivalent
20 to 25 °C
Lubricating oil 2190 TEP MIL-PRF-17331
120 to 122 °C
4.8.26.1 Observation. Any of the following shall construe specimen failure:
a.
A specimen tensile strength which is less than that specified (see 3.1).
b.
A specimen elongation which is less than that specified (see 3.1).
4.8.27 Toxicity index. The toxicity index shall be determined as specified in NES 713. For insulation
materials, the toxicity index shall be calculated on the mass of insulation on 1 meter length of finished wire size 22
AWG with a nominal wall thickness of 0.020 inch of insulation material. For jacket and filler materials, the toxicity
index shall be calculated on 100 grams of material. (The toxicity index is derived from the chemical analysis of the
product of combustion of the materials.)
4.8.27.1 Observation. Specimen failure shall be construed if any toxicity index is greater than that specified
(see 3.1).
4.8.28 Weathering. Jacket material shall be subjected to 720 hours of the xenon arc lamp weathering resistance
test in accordance with section 1200 of UL standard 1581.
4.8.28.1 Observation. Specimen failure shall be construed if the tensile strength and elongation retention is less
than 75 percent or if the specimen surface exhibits signs of cracking when examined using 3X magnification.
4.8.29 Tensile strength and elongation. Both aged and unaged specimens of the insulation and jacket material
shall be tested in accordance with Methods 3021 and 3031 of FED-STD-228. Unless otherwise specified on the
applicable specification sheet, there shall be 1-inch bench marks, 1 inch jaw separation and a rate of jaw travel of 10
inches per minute. For cross-linked polyethylene insulation meeting the criteria of ASTM D1248 for Types II, III,
and IV insulation the rate of jaw travel shall be 2 inches per minute. The thickness of the specimen shall be
measured using any suitable micrometer.
4.8.29.1 Observation. Specimen failure shall be construed if the tensile strength and elongation retention is less
than that specified herein or in the applicable specification sheet.
4.8.30 Shrinkage. A 12-inch specimen of cable shall be cut so that all components are flush at both ends.
Unless otherwise specified in the applicable specification sheet, the specimen shall then be aged at 136±3 °C for 6
hours in an air circulating oven. At the end of this period, the specimen shall be removed from the oven and allowed
to cool to room temperature. Shrinkage of the jacket shall then be measured to determine the total distance the
jacket has receded from both ends of the conductor.
4.8.30.1 Observation. Specimen failure shall be construed if the total shrinkage of the jacket is greater than
0.25 inch.
4.8.31 Crack resistance. This test shall determine the ability of glass braid covering to withstand bending and
to determine the propensity of glass braids to puncture overlaying covering.
49
For Parts Inquires call Parts Hangar, Inc (727) 493-0744
© Copyright 2015 Integrated Publishing, Inc.
A Service Disabled Veteran Owned Small Business