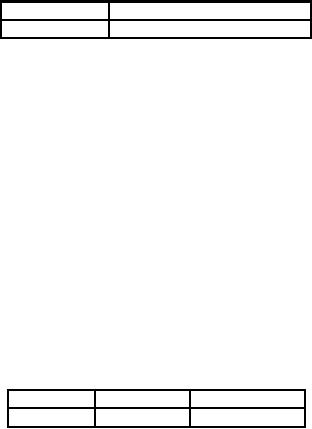
MIL-DTL-22759/90A
Humidity resistance: After humidity exposure wire shall meet the requirements for initial insulation resistance.
Identification of product: Not required for size 26. Color code designator not required.
Identification durability: 125 cycles (250 strokes), 250 grams weight.
Immersion (Test required for initial qualification only): Test in accordance with MIL-STD-2223 Method 1001
including the additional fluids listed in Table V of this specification. Use mandrels and weights listed in Table VI
for Bend testing. Dielectric test, 2500 volts (rms), 60 Hz. For turbine fuel immersion test of MIL-STD-2223, either
JP 4 or MIL-T-83133 type JP-8 (NATO Type F-34) may be used.
Impulse dielectric test: 8.0 kilovolts (peak). Test 100 percent of the wire
Insulation resistance: 5000 megohms for 1000 feet (min.)
Insulation State of Sinter: (Test required for qualification) Evaluate FP layers with a Differential Scanning
Calorimeter per ASTM D 4591.
Energy to Melt (Joules/gram)
First Heat
Less than 25 J/g
Life cycle: 500 hours at 290°C ± 2°C (554°F ± 3.6°F). Dielectric test, 2500 volts (rms), 60 Hz. Use mandrels
coated with polytetrafluoroethylene such that the diameter of the mandrels, after coating, still conform to the
required test mandrels diameters of table VI. After oven exposure, layers shall not separate and or tapes shall not
lift along the insulation or at the ends.
Low temperature (cold bend): Use mandrels and weights specified in Table VI. Chamber temperature , -65°C ±
2°C (-85°F ± 3.6°F). Dielectric test, 2500 volts (rms), 60 Hz.
Shrinkage: 0.091 inch (max.) at 290°C ± 2°C (554°F ± 3.6°F).
Smoke: 260°C ± 5°C (500°F ± 9°F); no visible smoke.
Solderability: Not required. This slash sheet is primarily intended for crimp terminations. For solderability
applications use the silver coated copper version of this specification.
Strippability: (Group II quality conformance test). Test in accordance with ASTM D 3032 section 27. The length
of the insulation slugs shall be 0.25 inches. There shall be no evidence of insulation left on the conductor when
viewed with the naked eye. The strip forces (lbs.) shall be as follows:
Wire Size
Min. Force
Max. Force
26-20
0.25 lb.
6.0 lbs.
Tape Overlap: In accordance with MIL-STD-2223, method 6005.
Tensile Modulus: Test composite film in accordance with ASTM D 882, Method A.
Thermal index: 260°C (500°F) minimum for 10,000 hours (Test required for initial qualification only). Test size
20 only in accordance with ASTM D 3032, Section 14.
Thermal shock resistance: Oven temperature, 260°C ± 5°C (500°F ± 9°F), Maximum change in measurement ,
0.091 inches. No cracking.
5