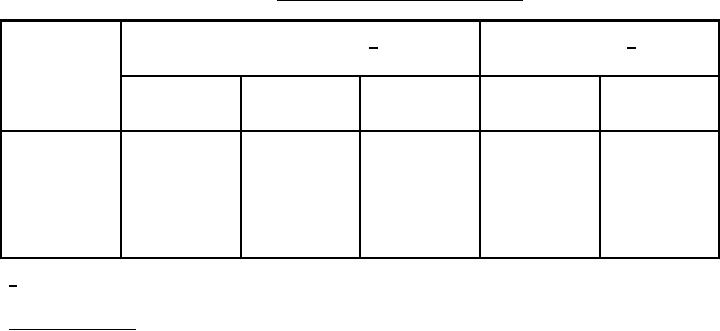
MIL-DTL-22759/83A
coated with polytetrafluoroethylene such that the diameter of the mandrels, after coating, still conform to the
required test mandrels diameters of table VI. After oven exposure, layers shall not separate and or tapes shall not
lift along the insulation or at the ends.
Low temperature (cold bend): Use mandrels and weights specified in Table VI. Chamber temperature , -65°C ±
2°C (-85°F ± 3.6 F). Dielectric test, 2500 volts (rms), 60 Hz.
Shrinkage: 0.125 inch (max.) at 230°C ± 2°C (446°F ± 3.6°F).
Smoke: 200°C ± 5°C (392°F ± 9°F); no visible smoke.
Solderability: Required.
Strippability: Not required.
Tape Overlap: In accordance with MIL-STD-2223, method 6005
Tensile Modulus: Test composite film in accordance with ASTM D 882, Method A
Thermal index: (Test required for initial qualification only). Qualification by similarity to MIL-W-22759/86.
Thermal shock resistance: Oven temperature, 200°C ± 2°C (392°F ± 3.6°F), Maximum change in measurement ,
0.125 inches. No cracking.
Wrap (mandrel wrap): No cracking, no dielectric breakdown. Use mandrels specified in Table VI. Dielectric test,
2500 volts (rms), 60 Hz.
TABLE VI. Test mandrel and test load requirements.
Test Mandrel Diameter 1/
Test Load 1/
Wire
(inches)
(lbs)
Size
(AWG)
Cold Bend
Life Cycle/
Wrap
Cold Bend
Life Cycle/
Bend Test
Bend Test
2
8.00
6.00
2.00
15.00
6.00
1
10.00
8.00
2.50
15.00
6.00
0
10.00
8.00
3.00
15.00
6.00
00
12.00
10.00
4.00
20.00
8.00
000
18.00
10.00
5.00
30.00
10.00
0000
18.00
10.00
6.00
30.00
10.00
Tolerance shall be ± 3 percent of the given values.
1/
Qualification of wire:
For qualification, a source is required to submit data on quality conformance tests and any finished wire tests as
required by the qualification authorization letter. All other testing will be performed by the qualifying activity at
the source's expense.
Due to the extended time period over which the thermal index test is performed, a source may become qualified
under this specification sheet while this test is still in progress.
5