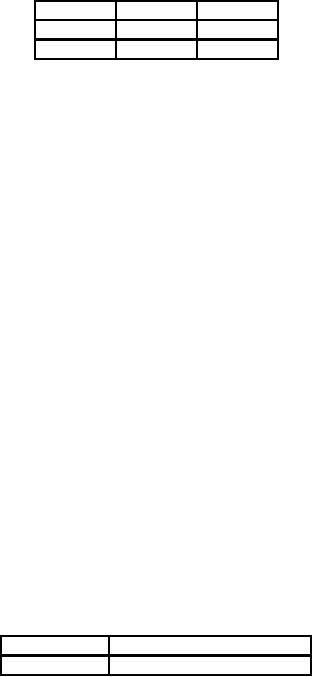
MIL-DTL-22759/80A
Dynamic cut- through (Test required for initial qualification only): Test in accordance with ASTM D 3032,
Section 22. Blade shall be the standard cutting blade except the cutting edge radius shall be .005 ± .001 inch.
Minimum average dynamic cut - through (lbs.) shall be as shown in the following table:
23 ± 5°C
150 ± 5°C
Wire Size
26
10 lbs.
8 lbs.
20
25 lbs.
20 lbs.
Flammability: Test in accordance with MIL-STD-2223, Method 1006, Procedure A:
Requirements:
Duration of after - flame 3 seconds (max.)
Flame travel
3.0 inches (max.)
No flaming of tissue
Forced Hydrolysis: (Test required for initial qualification only) 2000 hours at 70°C. Test 5 samples of AWG
size 20 only in accordance with SAE AS4373 method 602. All 5 samples must pass the dielectric test as listed in
method 602.
High frequency spark test: (When used in lieu of Impulse dielectric test) Test in accordance with MIL-STD-2223
Method 3008, 5.7 kilovolts (rms.) Test 100 percent of the wire.
Humidity resistance: After humidity exposure wire shall meet the requirements for initial insulation resistance.
Identification of product: Not required for size 26. Color code designator not required.
Identification durability: 125 cycles (250 strokes), 250 grams weight.
Immersion (Test required for initial qualification only): Test in accordance with MIL-STD-2223 Method 1001
including the additional fluids listed in Table V of this specification. Use mandrels and weights listed in Table VI
for Bend testing. Dielectric test, 2500 volts (rms), 60 Hz. For turbine fuel immersion test of MIL-STD-2223,
either JP 4 or MIL-T-83133 type JP-8 (NATO Type F-34) may be used.
Impulse dielectric test: 8.0 kilovolts (peak). Test 100 percent of the wire
Insulation resistance: 5000 megohms for 1000 feet (min.)
Insulation State of Sinter: (Test required for qualification ) Evaluate FP layers with a Differential Scanning
Calorimeter per ASTM D 4591.
Energy to Melt (Joules/gram)
First Heat
Less than 25 J/g
Life cycle: 500 hours at 230°C ± 2°C (446°F ± 3.6°F). Dielectric test, 2500 volts (rms), 60 Hz. Use mandrels
coated with polytetrafluoroethylene such that the diameter of the mandrels, after coating, still conform to the
required test mandrels diameters of table VI. After oven exposure, layers shall not separate and or tapes shall not
lift along the insulation or at the ends. ( Darkening of the tin coating of the conductors due to the normal air
oxidation shall not be cause for rejection of this test).
Low temperature (cold bend): Use mandrels and weights specified in Table VI. Chamber temperature , -65°C ±
2°C (-85°F ± 3.6°F). Dielectric test, 2500 volts (rms), 60 Hz.
Shrinkage: .091 inch (max.) at 230°C ± 2°C (446°F ± 3.6°F).
Smoke: 200°C ± 5°C (392°F ± 9°F); no visible smoke
5
For Parts Inquires call Parts Hangar, Inc (727) 493-0744
© Copyright 2015 Integrated Publishing, Inc.
A Service Disabled Veteran Owned Small Business