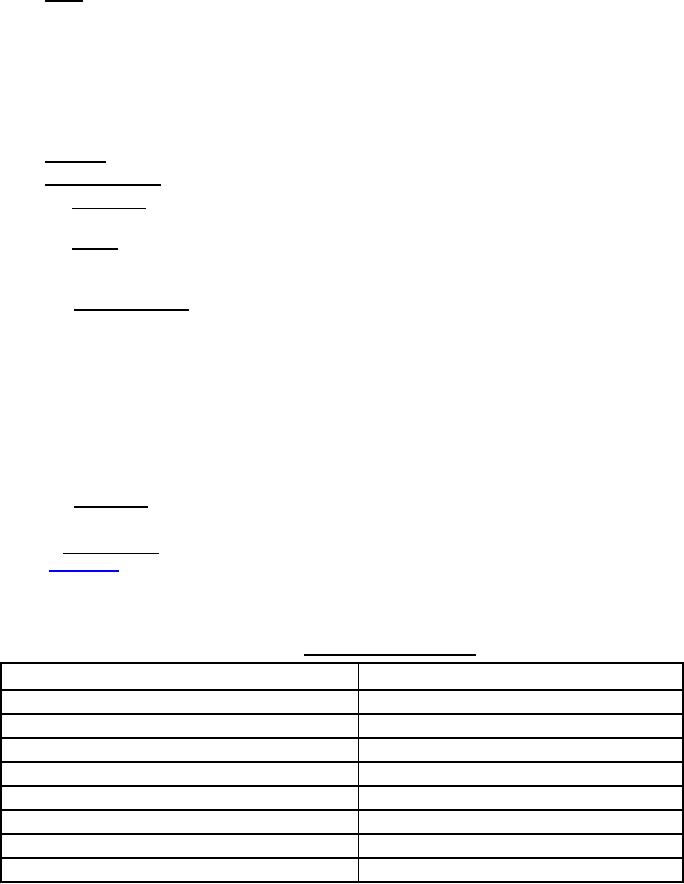
MIL-DTL-24640C
a. Jacket. Each specimen shall consist of a sufficient number of 75-millimeter long strips cut from the cable
jacket to completely cover the face area of the sample holder. To prevent excessive buckling and distortion of the
specimen during test, a wire mesh, manufactured from either a 1.0-millimeter diameter stainless steel wire with a
spacing of 12.5 millimeters and a square mesh configuration or a 40 mil stainless steel wire 2 mesh screen (2
openings per inch), shall be placed inside and across the face of the sample holder. The specimen shall be fabricated
by placing the specimen holder (with wire mesh) test face down onto a flat surface and positioning each 75-
millimeter length in the holder in a parallel arrangement so that when the holder is in the test position the strips will
be vertical. An insulating block 10 millimeters thick completely wrapped in aluminum foil shall be placed on top of
the strips followed by a tension spring and locking pin.
Insulation. The test specimen shall be a 1-meter length of 22 AWG finished wire.
b.
c.
Fillers and sealants.
(1) Non-fibrous. The test specimen shall be 3 by 3 inches of 0.070±0.010 inch thick block of the same
material used in the cable.
(2) Fibrous. The test specimen shall consist of as many 75-millimeter lengths of 0.070±0.010 inch
diameter strands necessary to fill the 3 by 3 inch test specimen holder one layer deep and as closely spaced as
possible. The test specimens shall be prepared as described in 4.7.17.1(a).
4.7.17.2 Special procedures. Special procedures shall include the following:
a.
Only the use of propane gas shall be allowed.
b.
The Radiometer shall be used to calibrate the heat flux at the initial start of each test period.
c. The test chamber shall be calibrated using a NIST CELLULOSE standard at the initial start of each test
period.
d.
The chamber shall be inspected to assure air tightness. Seals and gaskets shall be replaced as needed.
e. The test shall be run using a minimum of 3 specimens. If test values are below the limits specified (see
3.1), test is complete. If one test value deviates from the median value by more than 20 percent, two additional tests
shall be performed. The high and low test values shall be discarded and the remaining 3 averaged.
4.7.17.3 Observation. Specimen failure shall be construed if any smoke index is greater than that specified (see
3.1).
4.7.18 Immersion tests. Specimens of the cable jacket material (see 4.7.12.1) shall be immersed in the fluids
shown in table XVIII for 24 hours at the temperatures specified. The specimens shall then be removed, blotted to
remove excess fluid, then suspended in air at room temperature for not less than 3½ nor more than 4½ hours. Each
specimen shall be tested as specified in 4.7.21.
TABLE XVIII. Immersion test temperatures.
Fluid
Test temperature
Fuel oil, MIL-DTL-16884
98 to 100 °C
Turbine fuel, JP-5, MIL-DTL-5624
48 to 50 °C
Cleaner, isopropyl alcohol, ASTM D770
20 to 25 °C
Hydraulic fluid, MIL-PRF-83282 or MIL-PRF-87257
48 to 50 °C
Hydraulic fluid, MIL-PRF-17672
48 to 50 °C
Lubricating oil, MIL-PRF-23699
98 to 100 °C
Coolant, Monsanto Coolanol 25, or equivalent
20 to 25 °C
Lubrication oil, MIL-PRF-17331
120 to 122 °C
34
For Parts Inquires call Parts Hangar, Inc (727) 493-0744
© Copyright 2015 Integrated Publishing, Inc.
A Service Disabled Veteran Owned Small Business