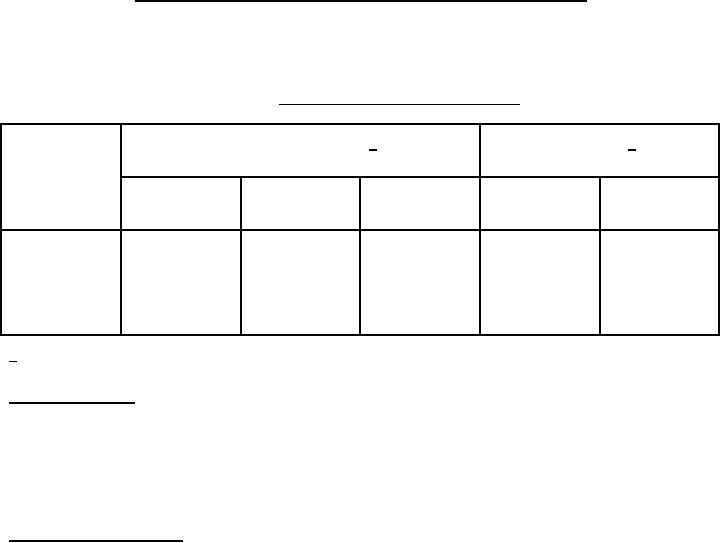
MIL-DTL-22759/82A
Tape Overlap: In accordance with MIL-STD-2223, Method 6005
Tensile Modulus: Test composite film in accordance with ASTM D 882, Method A
Thermal index: 260°C ± 5°C (500°F ± 9°F) minimum for 10,000 hours (Test required for initial qualification only).
Test size 20 only in accordance with ASTM D 3032, Section 14.
Thermal shock resistance: Oven temperature, 260°C ± 5°C (500°F ± 9°F), Maximum change in measurement ,
0.091 inches. No cracking.
UV Laser Marking: (Test required for initial qualification only) FP materials shall be formulated in such a manner
to achieve a 62 % minimum contrast level when marked by an Ultraviolet (UV) laser source operating at a delivered
power not to exceed 1.5 Joules/cm2. The contrast level is defined as
CL = (Reflectance of the background insulation - Reflectance of the laser mark) x 100
Reflectance of the background insulation
Wrap (mandrel wrap): No cracking, no dielectric breakdown. Use mandrels specified in Table VI. Dielectric test,
2500 volts (rms), 60 Hz.
TABLE VI. Test mandrel and test load requirements.
Test Mandrel Diameter 1/
Test Load 1/
Wire
(inches)
(lbs)
Size
(AWG)
Cold Bend
Life Cycle/
Wrap
Cold Bend
Life Cycle/
Bend Test
Bend Test
0.50
3.00
0.125
0.375
1.00
26
0.75
3.00
0.125
0.500
1.00
24
1.00
4.00
0.125
0.500
1.00
22
1.50
4.00
0.125
0.500
1.00
20
Tolerance shall be ± 3 percent of the given values.
1/
Qualification of wire:
For qualification, a source is required to submit data on quality conformance tests and any finished wire tests as
required by the qualification authorization letter. All other testing will be performed by the qualifying activity at the
source's expense.
Due to the extended time period over which the thermal index test is performed, a source may become qualified
under this specification sheet while this test is still in progress.
Changes from previous issue:
Marginal notations are not used in this revision to identify changes with respect to the previous issue due to the
extent of the changes.
6